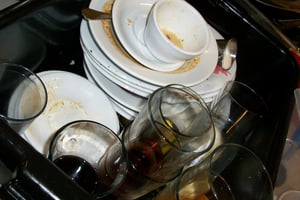
I worked on a purge savings project with a process engineer at custom injection molder earlier this year. He was producing both the cowls and bases out of Polystyrene (PS) in 2 different colors for a reputable manufacturer of fans. He was struggling to facilitate quick color changes, when going from black to white, and wanted to accelerate them. He expected their color changeover frequency to increase when these tools went from the “sampling stage” into “production.”
He was purging with a low-cost natural PS to try to address these black to white color changeovers and make them faster. While the cost of PS is on the cheaper side, it’s just a production resin designed to make parts and not designed to attack colorant and clean anything. Using production resin to clean your machine is like trying to wash dishes without soap.
PS may displace some of the previous colorant and resin from the machine, but nowhere even close to all of it. It generally ends up plugging right through the middle of the barrel/screw and pushes the previous colorant and resin to the side barrel walls and trialing edges of the screw flights. It layers over and masks everything, which ends up leading to contamination issues down the line and can make a bad situation even worse.
After a short technical discussion with the process engineer, I recommended he use our mechanical U Grade purging compound that’s specifically designed to attach itself to the previous colorant and attack it for a thorough, deep clean. We also reviewed our recommended mechanical purging instructions for injection molding to put him in a position to generate the best chance of success.
As a result of using the U Grade purging compound instead of using natural PS, the process engineer reported his color changeover process improved. He used approximately $90 worth of the purge to complete the color change, which reduced this downtime by 78% and lowered his scrap by 57%.
Learn more about improving your profitability with proper purging procedures.
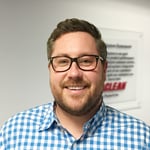
Ben Moore brings over 20 years of experience as a Purging Expert at Asaclean Purging Compounds, a leading manufacturer and distributor of purging compounds. As part of Asahi Kasei Plastics North America, Inc. (APNA), Ben has personally assisted hundreds of customers, helping them achieve significant cost savings. Based in Parsippany, NJ, Ben specializes in optimizing operations for thermoplastic injection molding, extrusion, compounding, and blow molding processes. His expertise lies in maximizing production efficiency by minimizing downtime and reducing scrap. For those interested in trying Asaclean products or seeking expert guidance, feel free to contact Ben directly. You can contact him at 800-787-4348, extension 227, or via email at bmoore@asaclean.com.
Comments