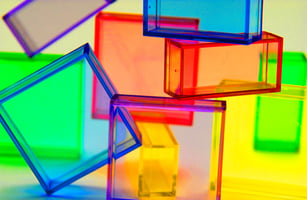
In Greek, the word Polymer by definition, means “many parts”, and it usually consists of a repeat unit joined together by what is known as a polymerisation reaction. Of course the nature of the polymer, being comprised of “many parts”, is what enables the existance of such a vast range of polymers, and the type of polymerisation they undergo is what allows us to manipulate their properties as desired.
I have talked before about how a simple and small change to the production process can give rise to a completely different end product- and if we take these small changes even further back to the polymerisation stage- we can see how so many plastics with such a vast range properties, are all manfactured from small variations of the same back-bone.
Most commodity plastics being used in todays industry (PE, PP, PVC and many more) are comprised from an ethene monomer, see below:
The image shows the ethene monomer. In this case where there are 4 (H) Hydrogen atoms attached to the (C) Carbon backbone, the end product of polymerization is -(CH4)n- polyethylene (as shown). The repeat monomer is what determines the polymer type and the breaking of the double-Carbon bond to create a link to the next C atom is what forms the backbone of the Polymer chain.
Following this, it is the type of poylmerisation (chain, branch, cross linking, etc.) and amount of polymersiation (number of links in the chain) that then go on to determine the properties of the polymer. i.e. molecular weight is determined by the length of the chain. But I’ll save the boring details on all that for another time.
When we receive our resin delivered to our production floor in its neat packaging, ready to simply open up and feed into our hopper for processing, how many of us actually visualise the granules as a long covalently bonded molecular chain?
Whether it’s PP, PVC, PE, PS, a high or low molceular weight product, whatever the complex polymer structure of that individual resin, when processing- we just see a tiny granule. A polymer bead appears to be a solid and stable structure, so it is important to remember, that as easily as that polymer chain has been created, it is just as easily broken.
The breakdown of that structure occurs via a process known as polymer degradation. Similar to the polymerisation reaction, there are many types of degradation (i.e. photo, chemical, mechanical, biological, thermal). During degradation, the polymer undergoes something known as chain scission, which is where the components of the long chain of molecules begins to breakdown into lots of smaller chains. There is one type of degradation that we are most susceptible to when it comes to polymer processing, and I will discuss that in more detail. This is called oxidation.
Oxidation takes place when the polymer encounters elevated temperatures in an enclosed environment where oxygen is present. Polymer processing, whether it be extrusion or injection molding, will both create this environment when a resin enters the machine to become molten. The only way to control oxidation is to eliminate the chance of oxygen entering the barrel. If the oxygen content is not controlled, it will give rise to degraded polymer which can cause production issues.
The most common cause for oxidation during processing is if the machine is left empty for a period of time- either an overnight or weekend shutdown or just for a few hours during production downtime.
If a machine is left empty for any period of time, this is when oxygen will enter the barrel. If there is any residue from the previous resin in the barrel, the oxygen and heat will lead to a breakdown of the molecular chain- we don’t see the chain scission on this level, but what we will see is the residue degrading into black specks. When you start production (after the machine has been left empty)- degraded material will appear through the die, contaminating your next production resin and increasing your waste. Sometimes the black specks are not noticed immediately. Instead, the degraded residue will build up and adhere to the screw over time. This can be more dangerous as it is extremely diffciult to remove and will require more timely pre-maintenace procedures.
To prevent oxidation a machine should NEVER be left empty, if you are shutting down overnight or just for a few hours, the barrel should be sealed, from the hopper to the die, ideally with a purging compound. Some processors are sealing with resin, although this prevents oxygen from entering, it still increases chances of residue on the screw, whereas a suitable purge compound, with low affinity to metal and high affinity to the polymer- will decrease any risks of residue and help eliminate cross contamination. If you suspect you already have a build up of degradation on your screw and you need to carry out a pre-mainteance procedure, a purge compound will also help make the screw pull a lot easier as the compound will lift away any residue from the screw with ease.
Oxidation is just one of the many types of degradation that polymers can undergo- but it can be controlled. With the knowledge of how oxidation occurs we can take the preventative action of sealing the machine (which is much more beneficial and less time consuming than the reactive action of pulling the screw). Quite often if we don’t visually see the issue we think it is not there, and that’s why by thinking of the polymer in its molecular state, it can help us to understand the polymers susceptibility. We can use this knowledge to ensure we take the right precautions needed to maintain and control the integrity of the Polymer and it’s “many parts.”
Discover ways to reduce thermoplastic molding scrap.
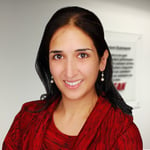
Kiran Raza is an Asaclean Purging Expert & Technical Sales Representative. She's worked in the plastics industry for nearly 20 years and has expertise In Bio-Medical Materials, Polymer Processing, and Materials Testing.
Comments