Introduction
In today’s competitive manufacturing environment, compounders are under constant pressure to reduce waste, improve changeover speed, and maintain consistent product quality. Whether you're compounding custom formulations or running high-volume engineering resins, production efficiency hinges on how well your equipment is maintained—and one often-overlooked opportunity is the use of high-performance purging compounds.
What is a Purging Compound, and Why Does it Matter for Compounders?
Purging compounds are specialized cleaning materials designed to remove residual polymers, colorants, carbon buildup, and contamination from extruders, twin-screw compounding lines, and downstream equipment. For operations professionals in compounding, they’re an essential part of preventive maintenance and changeover routines.
When you're switching from one formulation to another—especially with abrasive fillers or high-temperature resins—relying on virgin resin for changeovers can be costly, time-consuming, and ineffective.
Why Purging Compounds Are a Smart Move for Compounding Operations
- Minimize Downtime Between Runs
Whether you're switching materials, colors, or additives, unplanned downtime costs money. Using a purging compound reduces the number of screw pulls and shortens the transition window, getting your line back in production faster.
- Reduce Scrap and Improve Product Consistency
Scrap from black specks, color streaks, or contamination during startup or changeover can tank your margins. Purging compounds help eliminate residual material that causes defects, improving consistency across batches.
- Protect Equipment from Wear and Buildup
Compounding tough resins with glass fiber, flame retardants, or mineral fillers causes wear on screws and barrels. Regular purging prevents degradation and carbonization that can lead to premature equipment failure or expensive rebuilds.
- Support Lean Manufacturing Goals
For compounding facilities pursuing lean manufacturing or Six Sigma initiatives, reducing waste and increasing uptime are essential KPIs. A proper purging process contributes directly to these goals by supporting OEE (Overall Equipment Effectiveness).
- Simplify Preventive Maintenance
Scheduled maintenance windows are tight. Fast-acting, easy-to-use purging compounds let your maintenance and production teams clean machines without teardown, keeping PMs efficient and on schedule.
Who Benefits Most?
- Process Engineers looking to optimize changeovers
- Maintenance Managers responsible for minimizing unscheduled downtime
- Plant Managers focused on throughput and quality metrics
- Operations Leaders pursuing lean and continuous improvement initiatives
Key Compounding Applications Where Purging Makes a Difference
- Color changes between custom compounds
- Switching between filled and unfilled resins
- Cleaning high-temperature engineering plastics
- Carbon removal during planned shutdowns
- Routine cleaning of twin-screw extruders
Best Practices for Effective Purging in Compounding
- Use a dedicated purging compound—not regrind or virgin resin
- Match the purge type (chemical vs mechanical) to your materials
- Purge regularly as part of standard operating procedures (SOPs)
- Document results and track improvements in scrap rate and downtime
- Partner with a supplier who offers technical support and guidance
Conclusion
Purging compounds are more than a cleanup tool—they’re a process improvement strategy. For forward-thinking compounding professionals, they offer a way to hit production targets, reduce waste, and extend the life of capital equipment.
If you’re exploring how to improve your compounding line’s efficiency or reduce downtime between batches, learning how purging compounds fit into your process could be the key.
If you're dealing with slow changeovers, stubborn contamination, or unnecessary downtime, a small process improvement could make a big impact.
Ready to trial a new purge compound and experience the benefits for yourself? Get a free sample and schedule a meeting with an Asaclean purging expert to set up your onsite trial today. Our team is dedicated to helping you find the perfect purging solution for your needs, providing expert guidance and support every step of the way. Don't let another day go by without maximizing your efficiency and profitability – contact us now to get started on your journey to plastics processing excellence.
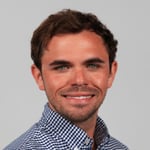
Tom Hanvey is the Product Manager for Sustainability for Asahi Kasei Plastics North America. Before joining APNA, he worked as the Senior Marketing Manager for Asaclean Purging Compounds. He's worked in the plastics industry for over 8 years and focuses on recyclable resins and on the inbound marketing side, providing easy-to-digest content to processors looking for an edge on their competition.
Comments