Introduction: The Hidden Key to Automotive Manufacturing Success
In today's highly competitive automotive injection molding industry, manufacturers face growing pressure to meet strict OEM requirements while staying profitable.
With increasing material complexity, frequent color changes, and tight production schedules, an ineffective purging process leads to unnecessary scrap, downtime, and quality issues.
The solution? A strategic purging program.
This blog covers:
✔ Why top-tier automotive suppliers rely on purging compounds
✔ How the right purge process reduces scrap and boosts machine efficiency
✔ The real cost of NOT having an optimized purge program
1. Meeting Stringent OEM Requirements
OEMs expect flawless, contamination-free parts.
A single defect can result in rejected shipments, costly rework, or lost contracts—all of which impact your bottom line.
✅ Why Purging Matters:
- Eliminates material contamination to prevent defective parts
- Ensures consistent production quality to meet OEM specifications
- Reduces color streaking and carbon buildup, keeping your parts pristine
💡 Example: An injection molder working with an EV manufacturer cut their contamination-related rejects by 37% after switching to a high-performance purging compound.
2. Ensuring Reliable, High-Quality Production
🔴 A single bad part can mean a recall.
🔴 Machine downtime means lost revenue.
In an industry where precision, safety, and consistency are critical, automotive manufacturers can’t afford machine inefficiencies.
How an Effective Purging Program Improves Production:
✔ Eliminates black specks, streaks, and color contamination
✔ Extends screw and barrel lifespan by preventing excessive buildup
✔ Reduces machine wear, ensuring reliable and long-lasting performance
📉 Results: Automotive manufacturers using Asaclean® see an average of 44% reduction in scrap and downtime—directly improving profitability.
3. Reducing Machine Changeover Downtime
🚗 The Problem: Frequent color and material changes slow down production.
As vehicle options expand, manufacturers must switch materials and colors quickly—but traditional purge methods waste time and material.
⏳ Without a purge program:
- Material transitions take 30–60+ minutes
- More wasted resin leads to higher costs
- Increased scrap rates result in lost revenue
⚡ With an effective purge program:
✔ Changeovers completed in 5–15 minutes
✔ 50%+ less material used per purge
✔ Minimal leftover contamination → Faster, cleaner transitions
🔎 Case Study: A Tier 1 supplier reduced their color change time from 42 minutes to 11 minutes—saving hundreds of hours per year in production time.
4. Extending Equipment Lifespan & Efficiency
💰 A poorly maintained machine costs you money.
Injection molding machines must run at peak efficiency to stay competitive. But over time, residual plastic, colorant buildup, and degraded material can lead to:
❌ Screw wear → Higher maintenance costs
❌ Carbon contamination → Defects & scrap
❌ Inconsistent cycles → Slower production
🔧 Purging prevents this.
✅ Regular purging keeps screws, barrels, and hot runners clean
✅ Reduces unplanned downtime & emergency maintenance
✅ Maintains processing consistency for tighter tolerances
🔍 Efficiency Tip: Purging compounds designed for hot runners help prevent carbon contamination in multi-cavity molds, ensuring perfect part quality.
5. The REAL Cost of Purging: Cost-per-Purge vs. Cost-per-Pound
📉 Many molders try to cut costs by using regrind or virgin resin instead of a dedicated purging compound. But this false economy leads to:
🚨 3–5x more material needed per purge
🚨 Longer machine downtime
🚨 Higher scrap rates
Cost Breakdown:
Purging Method | Material Used | Changeover Time | Scrap Rate | Cost Impact |
---|---|---|---|---|
Regrind/Resin | 3–5x more material | 30–60 min | High | Expensive in the long run |
Asaclean® Purging Compounds | Minimal usage | 5–15 min | Low | Maximizes efficiency & cost savings |
💡 Example: A manufacturer saved $28,000 annually by switching from regrind to Asaclean®—a 72% cost reduction in scrap and downtime.
Why Automotive Manufacturers Trust Asaclean®
📌 25+ years of expertise in automotive molding
📌 Industry-leading formulations for thermoplastics
📌 OEM-approved solutions used by Tier 1 suppliers
📌 44% average reduction in scrap & downtime
The Bottom Line:
✅ Less waste, fewer rejects, faster changeovers
✅ Lower maintenance costs & improved machine lifespan
✅ Increased efficiency & profitability
🔹 Is Your Facility Running at Maximum Efficiency?
Don’t let inefficient purging hold you back.
💡 Get expert guidance and a free purging consultation today!
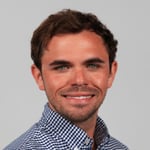
Tom Hanvey is the Product Manager for Sustainability for Asahi Kasei Plastics North America. Before joining APNA, he worked as the Senior Marketing Manager for Asaclean Purging Compounds. He's worked in the plastics industry for over 8 years and focuses on recyclable resins and on the inbound marketing side, providing easy-to-digest content to processors looking for an edge on their competition.
Comments