Estamos familiarizados con los dos tipos de cabezales de extrusión para moldeo por soplado: acumuladores (o intermitentes) y continuos. Si bien cada tipo tiene ventajas según el tamaño y la complejidad de la pieza, el tipo de resina, los tiempos de ciclo requeridos y otros factores, una de las mayores diferencias entre los tipos es la dificultad del proceso de purgado.
En general, el moldeo por soplado de extrusión es un proceso de menor presión que el moldeo por inyección, lo que nos deja con muy pocos parámetros de máquina para ayudar a un producto de purgado, ya sea de tipo mecánico o químico. Los tipos de cabezales de extrusión continua son bastante sencillos, ya que contienen cámaras y rutas de flujo de material que no suelen presentar muchos puntos de "estancamiento" como áreas de bajo flujo/baja presión. Generalmente, los bloques de alimentación o las zonas de distribución justo antes del cabezal presentan mayores desafíos de purgado. Aun así, el cabezal es relativamente más fácil de purgar al eliminar la resina para cambios de color/material o para la contaminación por carbón. Por otro lado, los tipos de cabezales acumuladores presentan un desafío específico: cómo manejar los puntos de estancamiento en la cámara del pistón.
La diferencia más significativa en el hardware es el pistón que se mueve verticalmente dentro de la cámara del cabezal, moviéndose hacia abajo desde un punto de ajuste (tamaño del disparo) para crear el parison del tamaño apropiado. La parte superior de la cámara, entre el pistón y las paredes, es donde el material se estanca más, causado por el movimiento ascendente del pistón al dosificar el disparo. Muchos de estos cabezales tienen "orificios de purga" cerca de la parte superior, lo que permite que el plástico degradado salga del cabezal a través de estos puertos. Una "línea" del tamaño del disparo se vuelve prominente dentro del cabezal durante carreras más largas. Durante una prueba reciente, trabajamos con el operador para definir qué puntos de ajuste tienden a mostrar la mayor contaminación de colores anteriores o material carbonizado/degradado atrapado en las partes superiores de la cámara, en otras palabras, encontrar esa "línea" donde se estanca el material. En este caso, ejecutaban una pieza más pequeña al 16% sin problemas y una pieza más grande al 30% sin problemas. Sin embargo, cuando el punto de ajuste/tamaño del disparo era del 65% o más grande, el material que salía a menudo estaba cargado con colores más antiguos de carreras anteriores e incluso manchas o trozos de contaminación por carbón. Concluimos que la "línea" es aproximadamente el 65% del tamaño del disparo.
Este conocimiento del historial de desechos nos ayudó a definir el mejor procedimiento para el purgado. Para esta aplicación, se prefería un purgado químico sobre un grado de purgado mecánico (fregado) debido a sus propiedades de expansión y generación de gas para acceder mejor a los puntos de estancamiento que un purgado mecánico tardaría demasiado en alcanzar. Para el purgado, decidimos llenar el cabezal en un punto de ajuste de aproximadamente 80% y disparar solo alrededor del 30%, restringiendo las posiciones del pistón solo entre 80% y 50%. Esto logró dos cosas:
- Elevar el punto de ajuste por encima de la "línea" objetivo del 65% permitió que el purgado accediera a la contaminación de arriba hacia abajo.
- Permitir que la reacción química limpiara desde arriba el área, mostrando la evidencia del estancamiento.
En segundo lugar, realizar disparos más cortos repetidos con solo un cambio neto del 30% en la posición del pistón consumió mucho menos purgado en lugar de desplazar repetidamente todo el 80%. Las líneas de color se eliminaron en 80 minutos, mejorando drásticamente sus típicos 8 a 10 horas perdidas al purgar con resina.
Las conclusiones principales aquí son: para purgar, cambie el punto de ajuste a una posición más alta que el punto mínimo donde aparece la contaminación, y realice solo disparos cortos mientras mantiene el cabezal relativamente lleno, evitando disparos de desplazamiento completo del cabezal para ahorrar en la cantidad de purgado.
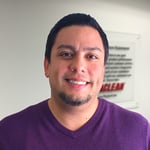
Celebrando su 24° año con Asaclean - Asahi Kasei Plastics North America, Lenny Gutiérrez es un reconocido experto en purgas que jugó un papel fundamental en la expansión de la compañía a México en 2009. Actualmente, se destaca como Representante Técnico de Ventas para Ohio, Illinois y Missouri. , combinando su amplio conocimiento de la industria con un enfoque estratégico para impulsar las ventas y las relaciones con los clientes. Lenny también es un destacado presentador en ferias y conferencias, y representa a Asaclean con su experiencia y profesionalismo.
Comentarios