En el blogs anteriores mencione dos tipos de purga y en una opinión personal en que proceso se comporta mejor cada uno. También se mencionó la frecuencia con la que se debe purgar. Lo que sigue es obtener el máximo posible del compuesto de purga seleccionado.
Esto se logra documentando bien en el sistema, cual se va a usar, para que casos, en qué cantidad y el método. Esta información la puede obtener en conjunto con su proveedor y adaptarla al detalle para su planta en específico. En el largo plazo el beneficio depende de la disciplina que se tenga para usar el material y la apertura para utilizar 2 o 3 purgas si fuera necesario. Cada una tiene una aplicación especial. “No se puede arreglar todo con solo una herramienta.”
En esta ocasión vamos a hablar de un caso real con una purga mecánica para inyección de plástico.
- Se determinó que la purga mecánica era la mejor opción para inyección, la variedad de resinas nos llevo a una purga de rango amplio de temperatura. Además se buscaba que la purga pudiera pasar por coladas calientes y sirviera como sello en los paros de máquina.
- Después que se comprobó que si es viable usar esta purga; se compra un lote pequeño y se introduce a la planta. En base a las anotaciones y experiencias registradas por el personal el resultado es un ahorro por menor tiempo muerto, sin embargo, consideran que se puede optimizar más el consumo de purga y reducirlo.
En un entrenamiento solicitado al proveedor se detectan parámetros que deben ajustarse en la máquina:
- Baja fuerza de la máquina por medio de las rpms, velocidad de inyección y contrapresión bajas.
- Tiros demasiado grandes llenando casi el 100% del barril. Siendo que puede ser al mínimo posible.
Se realiza un entrenamiento con personal de materiales, procesos de inyección, ajustadores y mantenimiento. Se revisan los parámetros críticos que en este caso son: rpms, velocidad de inyección, contrapresión y tamaño de disparo. También se les da una noción de la cantidad que se requiere en promedio para cada tamaño de máquina.
El Ingeniero de procesos documenta el método general y adapta en cada máquina sugerencias de los valores que deben usarse para cada parámetro según el tamaño de la máquina. Además de indicar la cantidad de purga máxima que se espera consumir en cada máquina.
El resultado es una limpieza igual de efectiva pero con un consumo menor casi del 50% del obtenido de las primeras veces en que se uso la purga.
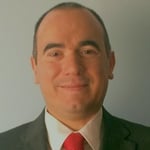
Héctor Sánchez, Gerente Nacional de Ventas de Asaclean - Asahi Kasei Plastics North America, aprovecha su amplia experiencia en procesamiento para ayudar a los extrusores y moldeadores a lograr sus objetivos operativos. Con un enfoque en reducir el desperdicio y aumentar las ganancias, el profundo conocimiento de Héctor sobre los compuestos de purga de Asaclean lo ha convertido en una figura fundamental en la industria. Más allá de su función principal, Héctor es un orador dinámico que comparte periódicamente sus conocimientos y estrategias en seminarios web y ferias comerciales en todo el país. Sus enfoques innovadores y su dedicación al éxito del cliente lo han establecido como un líder y mentor valioso en la industria del plástico.
Comentarios