When you use regrind or virgin resins to purge, the material creates another layer over any existing resins, color deposits or carbonized material within the barrel and on the screw. In time, these layers become additional sources of contamination, making purging even more difficult. Once your machine returns to production, carbonized materials eventually break free and contaminate your product. Twin-screw extruders cannot afford material or carbon contamination. Fortunately, these issues are easily avoided by selecting the appropriate purging compounds for your specific needs.
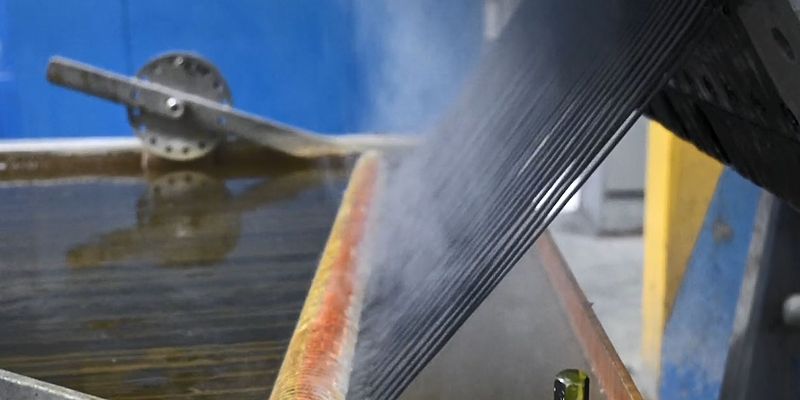
Contamination will occur regardless of your screw design. Adopting preventive purging practices not only saves your facility from machine downtime. It also reduces your scrap rates, customer rejects, and line shutdowns. You can’t afford to wait to run purging compounds until the last minute because, by that time, you’re already suffering from contamination issues or color streaks.
Using a purging compound at regular intervals prevents contamination from the beginning.
Typically, it only takes 1-2-barrel capacities of purging compound to prevent contamination. Preventative purging saves time and money through efficient use of capacity and prevents unplanned downtime.
There are three main benefits to implementing a preventive maintenance program and purging process at your facility:
- Preventing the buildup of carbon and color contamination
- Reducing excessive purging time and material waste at the end of production runs
- Limiting the frequency of screw pushes and minimizing the time and effort required to pull and manually clean your screw
3. Understand Your Mixing Areas & Screw Design
Earlier we touched upon how twin-screw extruders need to be incredibly customizable. They are modular to allow for screw combinations and feature unique mixing sections and some rather exotic machine settings. These factors, as well as the resins, additives, etc. are a perfect storm for contamination issues. If your line has additional feed streams, these issues occur even faster.
Because compounding is a continuous process, scrap occurs very quickly and often requires a teardown. Be conscious of your settings and collect data to understand how changes impact the MFR and processing temperatures of what you’re compounding. Extrusion is a low-pressure process so processors can’t manipulate pressures as they can in injection molding. Pay attention to venting. Plugging vents can help with purging. Pay attention to your settings and follow proper purging procedures to make sure you’re getting the best performance from your Asaclean®.
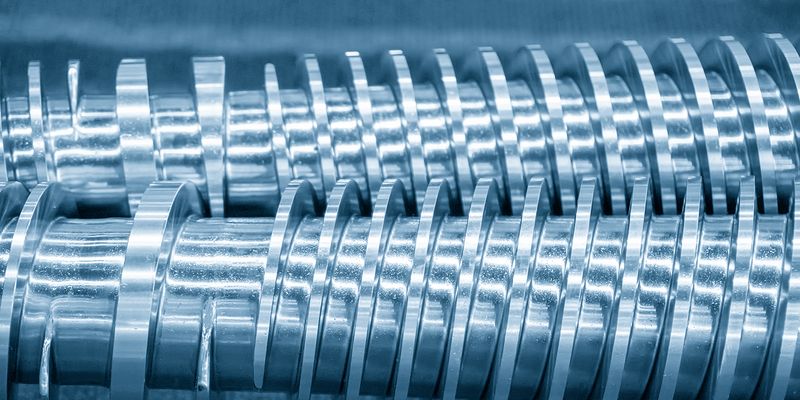
Also, we hear from many compounders who think that their screws are self-cleaning. Self-wiping is not the same as self-cleaning. Screw design does not have a significant impact on removing contamination.
4. Implement an Asaclean® Purge Program at Your Plant
Introducing a purge program can easily help compounders cut downtime by 50-75%. But when it comes to cleaning twin-screw extrusion equipment, there isn’t a one-size-fits-all process or purging-compound solution. Carbon builds up in your machine’s dead spots: mixing sections, dies, downstream equipment, etc. These are low-flow areas that would benefit from a chemical purging compound. But if you are dealing with frequent teardowns, a strong cleaner might be needed as well.
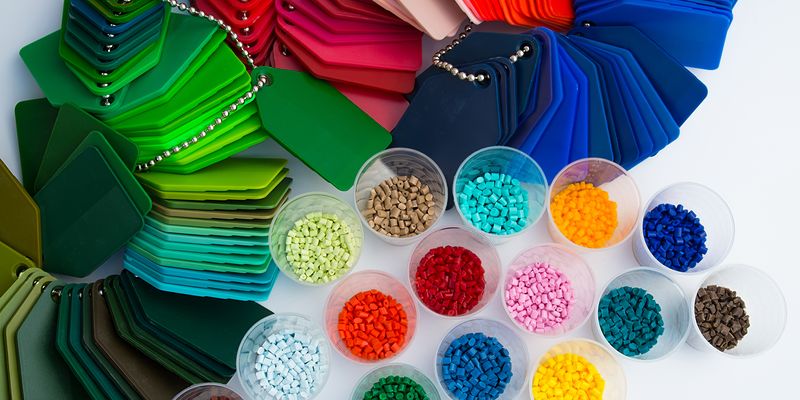
Without the right purging compound and procedures, you run the risk of increased reject rates. However, determining the proper purging compound grade is not simply about eliminating color and carbon contamination—it’s also about the impact on your bottom line. Taking a holistic approach will help you improve efficiency and profitability.
Request your free 10-minute purging consultation with an Asaclean® Purging Expert and set yourself up for success today. When you reach out to a purging expert for a free consultation, they will look at several key things to consider in order to select the right grade and quantities necessary to choose the best purging compound for your system.
5. Optimize Your Screw Pushes for Quicker & Easier Teardowns
Sometimes a change in product requires you to swap out a screw element, and this can be time-consuming if the screws are not in an ideal condition for removal. Asaclean® has several large compounding customers who run several resins or the same resin with different additives. Often compounding different resins requires different screw designs or the compounder is required to pull screw to ensure processing resins don’t mix. Most polymers by nature tend to adhere to screw surfaces, and these layers present challenges not only for screw cleaning but also for screw removal.
A typical compounder may pull a screw four to five times a week. Those producing color masterbatches are likely to pull screws every day. Some plants may carry duplicate screws, but these can cost tens of thousands of dollars in additional capital expense. For most compounders, pulling a screw and cleaning it may be the only option to get back into production. This process can be labor-intensive and incredibly costly since downtime can cost upwards of $1000 to $1200/hr. It’s not uncommon for compounders to struggle with 8-12-hour screw pushes. Built-up material on screw flights is very difficult to remove. You need a solution that removes the need to clean the screw by baking it in an oven, by using wire brushing, torching, etc. These secondary processes also raise the likelihood of injury or of accidentally breaking an expensive screw component.
Compounders push screws for three main reasons:
- They may be required to ensure 100% no polymer cross-blending
- Changeovers require a different screw design
- Severe contamination cannot be removed by normal purging.
Although screw pushes might be necessary in your plant, that doesn’t mean they need to be time-consuming, profit-sucking headaches. There are purging compounds specifically engineered for screw pulls/pushes. Screw pushes using Asaclean® EX Grade often save processors 75-90% on downtime.
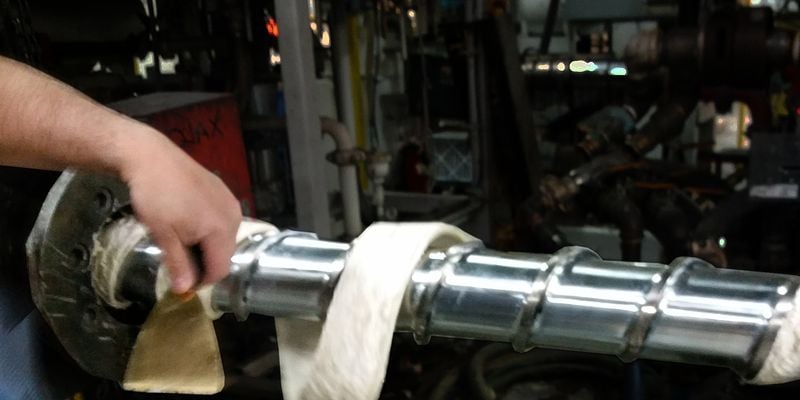
6. Seal Your Machine With Asaclean® Purging Compounds During Every Shutdown
Aside from regular and preventative-maintenance purging, use a heat-stable purging compound like Asaclean NCR Grade for temporary or extended shutdowns and sealing, especially over weekends or holidays.
During a shutdown without purge, oxidation occurs which causes contamination, delaying startups and resulting in extended machine down. NCR creates an “air-tight” time and scrap environment in the barrel and promotes further cleaning during the shutdown.
Request your free 10-minute purging consultation with an Asaclean® Purging Expert and set yourself up for success today. When you reach out to a purging expert for a free consultation, they will look at several key things to consider in order to select the right grade and quantities necessary to choose the best purging compound for your system.