In plastics processing, some losses are an unavoidable part of the manufacturing process. However, hidden inefficiencies and unnecessary delays can lead to significant production losses and increased costs. Identifying and addressing these issues is key to improving efficiency and maximizing profits.
The Challenge: A Costly Mold Startup Process
A plastic injection molding company supplying the automotive industry faced recurring production delays. They used a hot runner mold to produce rear camera components, processing PEI resin at 390°C. Every time they set up the mold, they encountered a major issue—material flow was blocked, preventing startup.
To fix this, the mold had to be removed and cleaned manually, requiring two mold technicians and 12 hours of labor. Since leaving a machine idle was not an option, the team scrambled to install a different mold, involving additional technicians, assemblers, and planners.
Instead of a smooth one-hour startup process, the company endured:
- Repeated mold changes—assemblers had to remove and reinstall the mold multiple times.
- Lost technician time—mold specialists were pulled from maintenance and other essential tasks.
- Unplanned schedule adjustments—setup technicians and planners had to reorganize production, causing further disruptions.
- Machine downtime—delayed production resulted in financial loss and inefficiency.
The Solution: A Simple Yet Effective Fix
To solve this problem, the company’s process engineer tested various strategies. The most effective solution was sealing the mold with Asaclean® PF before shutdown.
By purging the mold with a high-temperature purging compound before storing it, they eliminated contamination and blockages. When it was time to restart production, the mold was ready to run immediately without extra cleaning or wasted labor.
How Much Is Lost Time Costing Your Business?
Think about the impact of unnecessary delays in your own operation:
- How much time do your mold technicians, process technicians, assemblers, or planners spend solving avoidable startup issues?
- What is the cost of lost production time and missed deadlines?
- How much more efficiently could your team work with a proactive solution?
Preventing startup issues with a simple purging procedure can drastically reduce downtime and labor costs, allowing your team to focus on production instead of troubleshooting.
Stop wasting time—implementing the right process improvements can make all the difference in your bottom line.
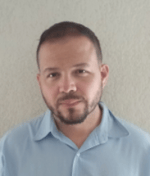
Mario De León brings unparalleled experience as a Technical Sales Representative for Mexico, with a career in the plastics processing industry spanning every key position, from materialist to injection molding management. With more than two decades of experience, Mario has mastered the art of team leadership by sharing the acquired knowledge with love and a desire for growth. Recognized for building lasting relationships in the industry, his dedication to improving clients' operations and driving success demonstrates his invaluable contribution to our team and the plastics industry.
Comments