Starting up after weekends and holidays is notorious for its increased downtime and scrap, presenting significant challenges for process engineers, quality control experts, and plant management. This phase often leads to wasted resources and raises the potential for contaminated parts to reach customers, resulting in complaints and rejections. Notably, scrap rates during the initial hours of startup, especially on Mondays, can surge to as much as 90% of production. Addressing this, we offer 4 strategic tips as part of a comprehensive preventive purging program, aimed especially at those working with temperature-sensitive polymers such as PVC, Acetal, and flame retardants, as well as complex resins like PBT, nylon, acrylic, and polycarbonate.
1. Proactive Use of Purging Compounds
Preventing resin degradation and the deterioration of additives or pigments starts with the proactive use of purging compounds. Select compounds that can remain within the barrels, screws, and system overall, effectively blocking oxygen ingress, which fuels degradation. This approach guarantees a thermally stable material ready to withstand residual heat during machine cooldowns or heat-ups, significantly reducing the risk of degradation.
2. Heater Shutdown During Inactivity
Unnecessary heater operation can provoke severe degradation, risking equipment damage or even causing the plastic to ignite. Turning off heaters when not in use is crucial; it not only prevents potential safety hazards but also aids in avoiding the formation of layers that detach as black spots during production. The time saved by quick temperature ramp-ups is far outweighed by the hours spent cleaning machines or addressing contamination issues. Utilizing the contraction effect of purging compounds during heater shutdown can also aid in dislodging forming contaminants.
3. Efficient Purging Between Batches
Ensuring a thorough purge of the barrel and mold after completing a production batch and before transitioning to another is essential for maintaining quality. Proper immediate purging prevents the onset of contamination, allowing production to resume smoothly without quality issues, thus maintaining high customer satisfaction levels.
4. Structured Machine Startup
A disciplined approach to machine startups can further reduce scrap. Organize the startup sequence by prioritizing machines based on urgency and operating temperatures. For high-temperature processes, a gradual temperature increase is advised to prevent the formation of layers and black specs, optimizing startup efficiency.
Integrating these four tips into a preventive purging strategy can dramatically reduce scrap during startups, enhancing operational efficiency and reducing waste. For those interested in experiencing these benefits firsthand, requesting a free sample of our purging compounds is an excellent starting point.
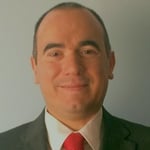
Hector Sanchez, the National Sales Manager at Asaclean - Asahi Kasei Plastics North America, leverages his extensive processing expertise to assist extruders and molders in achieving their operational goals. With a focus on reducing scrap and increasing profits, Hector's in-depth knowledge of Asaclean's Purging Compounds has made him a pivotal figure in the industry. Beyond his primary role, Hector is a dynamic speaker, regularly sharing his insights and strategies at webinars and tradeshows nationwide. His innovative approaches and dedication to customer success have established him as a valued leader and mentor in the plastic industry.
Comments