3 Tips for Better Production Runs in Profile Extrusion
1. Don’t Use Production Resin for Changeovers or to Purge Your Extruder
Historically, we’ve talked to processors who look at the price of the production resin and tell us that they’re okay taking a little longer on changeovers because the cost of resin is cheap. Over time you will have contamination issues that will bring production to a screeching halt. Production resins are not designed to clean machines and are not a substitute for commercial purging compounds.
Purging your extruder with the next resin or regrind is time-consuming, wasteful, and ineffective at removing color and carbon contamination. While you might think you’re running good product, a few things are happening that will cause much bigger headaches down the road.
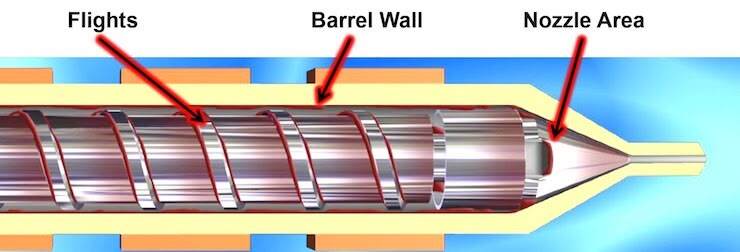
First, although you don’t see it happening, your resins are layering within your screw, barrel, and die. Eventually those layers will break off and cause contamination issues that will require a teardown.
Second, your output will decrease. Many processors call our team looking for answers about why their output dropped. Usually, this has to do with conditions changing within the screw and barrel.
Third, you are unnecessarily wasting time on changeovers, and production resins are too expensive to justify hundreds or thousands of pounds of scrap.
The cost of production resin isn’t so cheap anymore, and supply-chain issues make commodity and engineering resins much harder to come by.
You can’t afford to waste production material. It’s scarce and costly.
2. Be Proactive—Not Reactive—When it Comes to Purging
Many extruders only use purging compounds when it’s absolutely necessary. But engaging in this type of purging “process” leads to reduced profitability and efficiency.
Adopting preventive purging practices not only saves your facility from machine downtime. It also reduces your scrap rates, customer rejects, and line shutdowns. You can’t afford to wait to run purging compounds until the last minute because, by that time, you’re already suffering from contamination issues or color streaks.
Using a purging compound at regular intervals prevents contamination from the beginning. Typically, it only takes 1-2-barrel capacities of purging compound to prevent contamination. Preventative purging saves time and money through efficient use of capacity and prevents unplanned downtime.
There are three main benefits to implementing a preventive maintenance program and purging process at your facility:
- Preventing the buildup of color and carbon contamination
- Reducing excessive purging time and material waste at the end of production runs
- Limiting the frequency of screw pushes and minimizing the time and effort required to pull and manually clean your screw
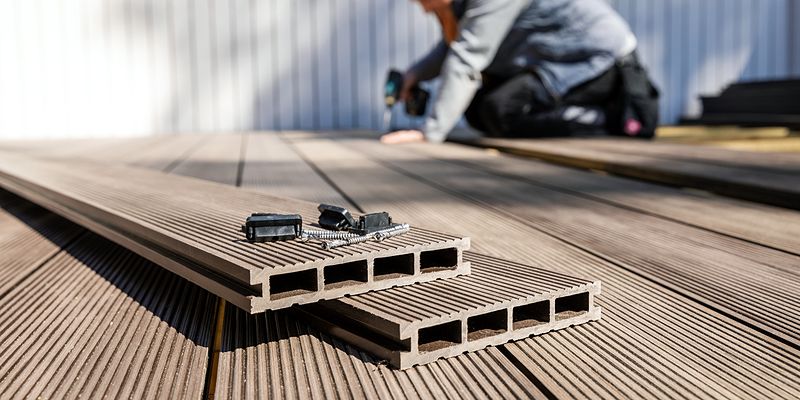